| 25 años generando CONFIANZA
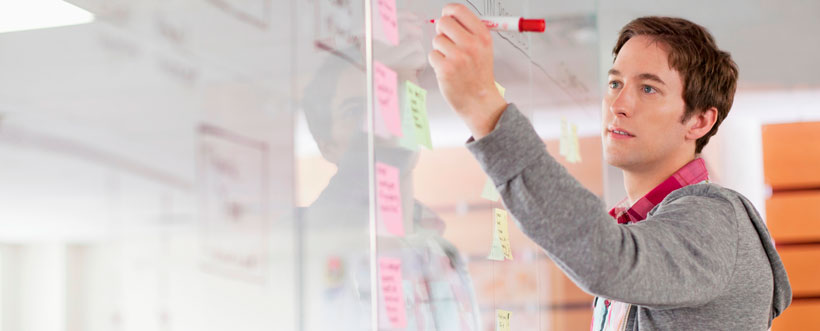
Índice de contenidos
Toggle¿Cuál es el origen del Método de las 5 S?
El diseño del Método de las 5 S se adjudica al ingeniero japonés Kiichiro Toyoda, fundador de la compañía de automoción Toyota. El método surge como una opción a la cadena de montaje utilizada en las factorías de Ford, alrededor del mundo. El objetivo inicial fue construir espacios de trabajo productivos y seguros, en contraposición con una cadena de montaje que generaba problemas, accidentes y conflictos entre los trabajadores, característica de las fábricas de Ford. Es importante entender el contexto histórico en el que aparece el Método de las 5 S. Europa y el lejano oriente apenas se reponían de la Segunda Guerra Mundial, en la década de los cincuenta. Las organizaciones necesitaban ser eficientes, minimizar costes y mejorar cada día más. Las cinco S, corresponden a las iniciales de cada una de las etapas que conforman el Método, en el idioma japonés. Veamos cuáles son y qué hay que hacer en cada una de ellas.¿Cuáles son las etapas del Método de las 5 S?
El método se desarrolla en cinco etapas, cada una distinguida por una palabra en japonés: Seiri (Ordenar), Seitón (Organizar), Seiso (Brillar), Seiketsu (Estandarizar), Shitsuke (Sostener). Cada uno de los componentes tiene relevancia por sí solo. Pero, unidos, el resultado individual se potencia para entregar los resultados que han hecho famoso el Método de las 5 S. Cada etapa se desarrolla así:1. Ordenar (Seiri)
Un lugar de trabajo ordenado, seguro y, por tanto, productivo, alberga tan solo los instrumentos y las herramientas necesarios para el trabajo que allí se desarrolla. Y estos elementos deben estar clasificados y etiquetados por color: rojo para lo que puede desecharse o almacenarse lejos del espacio de trabajo y amarrillo para las herramientas indispensables que deben permanecer en el lugar de trabajo.2. Organizar (Seiton)
Los artículos etiquetados con amarillo, debido a que son indispensables, deben organizarse y clasificarse de acuerdo con la frecuencia de uso, el tamaño, las precauciones especiales para su uso, u otra condición similar. La idea es ajustar la disponibilidad de los elementos que se utilizan con mayor frecuencia, pero también aprovechar al máximo el espacio, dejando áreas libres para el desplazamiento seguro de las personas.3. Limpiar (Seiso)
Con el puesto de trabajo liberado de elementos innecesarios, y con las herramientas que se utilizan organizadas, clasificadas y etiquetadas, el siguiente paso lógico es limpiar y asear el sitio con supremo esmero. Es importante eliminar y prevenir fugas de agua que ocasionen suelo mojado, derrames de aceites o de grasas, elementos en el suelo que pueden causar resbalones o caídas.4. Estandarizar (Seiketsu)
El objetivo en esta etapa es hacer de cada uno de los tres pasos anteriores, una costumbre: esto es, estandarizar. Los estándares no solo funcionarán para las tareas de organización, clasificación y aseo. Los procesos de trabajo o de gestión que se lleven acabo en el lugar, también necesitan ser estandarizados. Es importante que este paso se documente y se expresen en términos gráficos y en textos, los procesos, los horarios, flujos de trabajo, listas, elementos a utilizar…5. Sostener (Shitsuke)
El último paso es el que garantiza la sostenibilidad del modelo y la mejora continua que lo caracteriza. En cierto modo, el método de las 5 S tiene puntos de unión con el modelo PDCA. La operación cíclica, continua, revisando, auditando y corrigiendo, es la forma en la que se asegura la sostenibilidad y la mejora del método. El Método ha sido diseñado para operar en cualquier espacio de trabajo, y con cualquier tipo de proceso. Sin duda, la seguridad laboral no es la excepción. En esta área en particular, el desarrollo del Método requiere información, resultado de procesos de automatización. Una solución adecuada para aportar ese componente tecnológico, es la que mencionamos a continuación.Software HSETools
El Software HSETools es una solución modular, basada en la nube, diseñada para atender todas las necesidades en cuanto a Gestión HSE de las organizaciones. Esta plataforma incorpora módulos para la Gestión de Incidentes y Accidentes, Inspecciones y Checklist, Gestión de Riesgos, Programas HSE… Conócelos el próximo martes, en nuestra DEMO Online gratuita.¿Desea saber más?
Entradas relacionadas
27/08/2025
La fatiga laboral y los problemas de salud mental representan uno de los mayores retos para los responsables…
25/08/2025
Un Software de Gestión de Incidencias es una herramienta imprescindible para organizaciones que buscan profesionalizar su enfoque en…
20/08/2025
El cumplimiento normativo es prioritario en la gestión de contratistas. En ese camino, la gestión documental CAE (Coordinación…
18/08/2025
La transformación digital ha revolucionado la gestión empresarial en todos los sectores y el ámbito de la seguridad,…